BASF Chemical Plant
- Isomag
- Oct 22, 2016
- 1 min read
Isomag bearing isolators solve contamination issues for centrifugal pump applications in chemical processing plants.
In 1986, Al Newburn, the Manager of the recently formed Reliability Department at BASF Chemical in Geismar, Louisiana began testing labyrinth seals vs magnetic face bearing isolators on forty (twenty labyrinth, twenty magnetic face) ANSI pumps in the Toluene Di-Isocyanate (TDI) Unit. The Reliability Team monitored pump bearing oil contamination through sampling, and pump bearing vibration for four years. Credible results showed:

Bearing housings with labyrinths averaged two oil changes per year due to ingress of contaminants. Bearing housings with magnetic face bearing isolators averaged one oil change every three years. Bearing changes on labyrinth housings averaged 14 months, bearing changes on magnetic bearing isolator housings increased to 48 months. In 1996 instead of staying with industry standard labyrinth isolators, BASF wrote a site “GMR-48” bearing housing specification which included the Isomag RSA seals. Today’s Geismar specifications includes Isomag’s V7-UL seals on their centrifugal pumps. In 2017 BASF’s Geismar site continues to target ultra-clean oil as very significant to increased bearing life. Isomag bearing isolators continue to play a valuable role. BASF/Geismar is one of Isomag’s original customers beginning in 1994. For over 20 years this facility has upgraded thousands of pumps and gearboxes that are in service today. Their annual spend to Isomag in maintaining ultra-clean oil in thousands of upgrades is less than $30K per year for the last ten years.

Application Summary:
Problem solved: Bearing oil contamination
Previous bearing protection:
labyrinth isolators
Upgraded to: Isomag RSA ,
MP V7 - UL
Application: ANSI Pumps
Units sold: 8,000+
www.chemical-technology.com

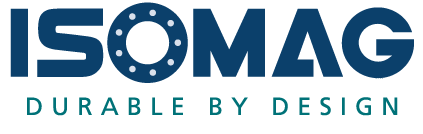
Comments